Case Studies
Viterra Bulk Fertilizer Bins
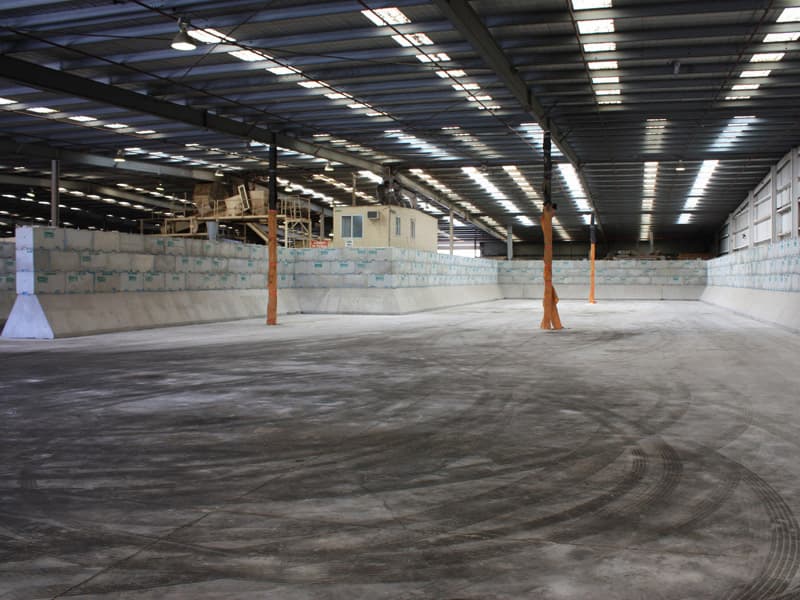
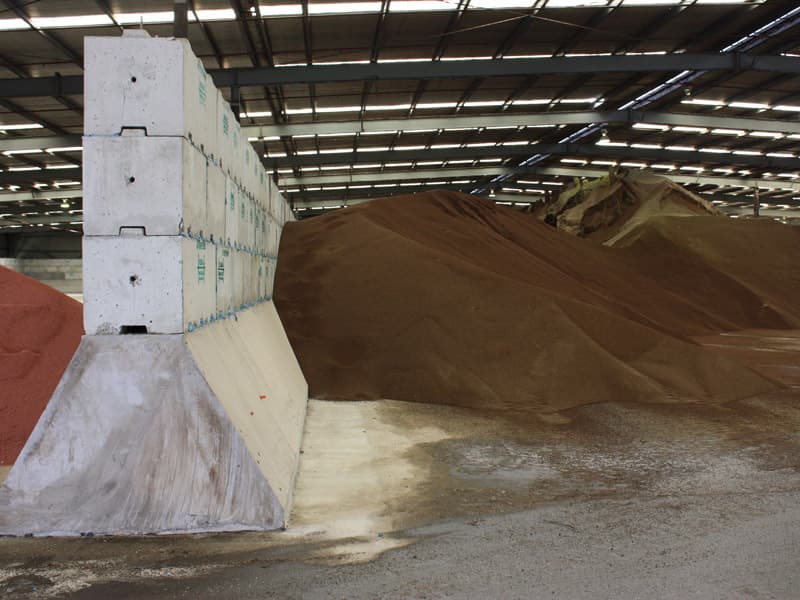
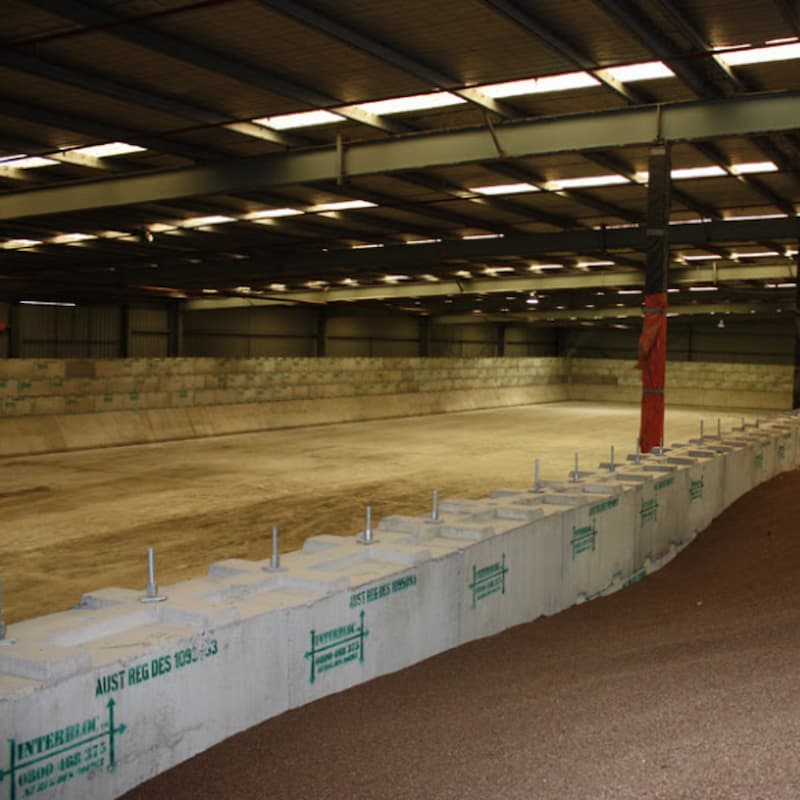
The Challenge
Viterra operates in North America, Australia, New Zealand, and China. The company, based in Regina, Saskatchewan, is structured into three business units, including an agri-products division that manufactures and sells fertiliser.
Storing bulk fertiliser is not straightforward. If left unchecked, its weight can push out the sides of the large tin sheds typically used to store agricultural nutrients. To prevent this, fertiliser suppliers construct robust internal retaining walls to absorb the pressure around the building's edges and to separate different types of fertiliser.
Agri-business giant Viterra had already installed retaining walls at its fertiliser stores in Geelong and Adelaide but encountered health and safety issues with conventional building techniques. An additional complication was that the landlord of its 150 by 70 metre Geelong store insisted Viterra could only use removable materials to construct retaining walls, without causing permanent damage to the building's concrete slab floor.
The Solution
Rohan Pollard of Blueprint Consulting Engineers explained that Viterra was exploring several options and required an engineer-designed system with removable walls. "Interbloc provided exactly what Viterra needed at a price they were comfortable with. The solution exceeded Viterra's requirements in every way," Pollard stated.
Health and safety were of utmost importance. "The Interbloc approach doubled the safety factor at the stores, which was crucial for Viterra. As a large company, Viterra needed assurance in its health and safety systems. The company wanted a solution compliant with the code, as its existing walls were under strength and under capacity," Pollard emphasised.
In total, there are now 1.2 kilometres of Interbloc walls across the two sites. This involved shipping approximately 3,000 tonnes of blocks from New Zealand, along with 45 tonnes of reinforcing steel, and pouring 1,700 cubic metres of concrete.